Plākšņu sadalīšanas tehnoloģija kā kritisks solis pusvadītāju ražošanas procesā ir tieši saistīta ar mikroshēmas veiktspēju, ražību un ražošanas izmaksām.
#01 Vafeļu griešanas pamatinformācija un nozīme
1.1 Vafeļu griešanas kubiņos definīcija
Plākšņu sadalīšana kubiņos (pazīstama arī kā iegravēšana) ir būtisks solis pusvadītāju ražošanā, kura mērķis ir sadalīt apstrādātās plāksnītes vairākās atsevišķās matricās. Šīs matricas parasti satur pilnīgu shēmas funkcionalitāti un ir galvenās sastāvdaļas, ko galu galā izmanto elektronisko ierīču ražošanā. Tā kā mikroshēmu konstrukcijas kļūst sarežģītākas un izmēri turpina samazināties, plākšņu sadalīšanas tehnoloģijas precizitātes un efektivitātes prasības kļūst arvien stingrākas.
Praktiskajās darbībās vafeļu griešanai parasti tiek izmantoti augstas precizitātes instrumenti, piemēram, dimanta asmeņi, lai nodrošinātu, ka katra matrica paliek neskarta un pilnībā funkcionāla. Galvenie soļi ietver sagatavošanu pirms griešanas, precīzu kontroli griešanas procesa laikā un kvalitātes pārbaudi pēc griešanas.
Pirms griešanas plāksne ir jāmarķē un jānovieto, lai nodrošinātu precīzus griešanas ceļus. Griešanas laikā stingri jākontrolē tādi parametri kā instrumenta spiediens un ātrums, lai novērstu plāksnītes bojājumus. Pēc griešanas tiek veiktas visaptverošas kvalitātes pārbaudes, lai nodrošinātu, ka katra mikroshēma atbilst veiktspējas standartiem.
Plākšņu griešanas tehnoloģijas pamatprincipi ietver ne tikai griešanas iekārtu izvēli un procesa parametru iestatīšanu, bet arī materiālu mehānisko īpašību un raksturlielumu ietekmi uz griešanas kvalitāti. Piemēram, zema k dielektriskā silīcija plāksnītes to sliktāko mehānisko īpašību dēļ ir ļoti jutīgas pret sprieguma koncentrāciju griešanas laikā, kas noved pie tādiem bojājumiem kā šķembošana un plaisāšana. Zema k materiālu zemā cietība un trauslums padara tos vairāk pakļautus strukturāliem bojājumiem mehāniska spēka vai termiskās slodzes ietekmē, īpaši griešanas laikā. Instrumenta un plāksnītes virsmas saskare apvienojumā ar augstu temperatūru var vēl vairāk saasināt sprieguma koncentrāciju.
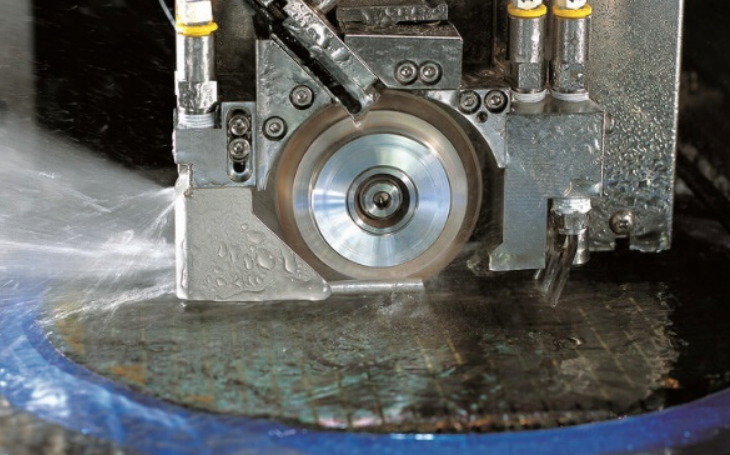
Līdz ar materiālzinātnes sasniegumiem vafeļu griešanas tehnoloģija ir paplašinājusies ārpus tradicionālajiem silīcija bāzes pusvadītājiem, iekļaujot jaunus materiālus, piemēram, gallija nitrīdu (GaN). Šie jaunie materiāli, pateicoties to cietībai un strukturālajām īpašībām, rada jaunus izaicinājumus griešanas procesiem, kas prasa turpmākus griešanas instrumentu un metožu uzlabojumus.
Kā kritisks process pusvadītāju nozarē, vafeļu sadalīšana kubiņos turpina tikt optimizēta, reaģējot uz mainīgajām prasībām un tehnoloģiskajiem sasniegumiem, liekot pamatu nākotnes mikroelektronikas un integrēto shēmu tehnoloģijām.
Uzlabojumi vafeļu sadalīšanas tehnoloģijās sniedzas tālāk par palīgmateriālu un instrumentu izstrādi. Tie ietver arī procesu optimizāciju, iekārtu veiktspējas uzlabošanu un precīzu sadalīšanas parametru kontroli. Šo uzlabojumu mērķis ir nodrošināt augstu precizitāti, efektivitāti un stabilitāti vafeļu sadalīšanas procesā, apmierinot pusvadītāju nozares vajadzības pēc mazākiem izmēriem, augstākas integrācijas un sarežģītākām mikroshēmu struktūrām.
uzlabošanas zona | Īpaši pasākumi | Efekti |
Procesu optimizācija | - Uzlabot sākotnējos sagatavošanās darbus, piemēram, precīzāku vafeļu pozicionēšanu un ceļa plānošanu. | - Samazina griešanas kļūdas un uzlabo stabilitāti. |
- Samazina griešanas kļūdas un uzlabo stabilitāti. | - Izmantojiet reāllaika uzraudzības un atgriezeniskās saites mehānismus, lai pielāgotu instrumenta spiedienu, ātrumu un temperatūru. | |
- Zemāks vafeļu lūzuma līmenis un uzlabota mikroshēmu kvalitāte. | ||
Iekārtu veiktspējas uzlabošana | - Izmantot augstas precizitātes mehāniskās sistēmas un progresīvas automatizācijas vadības tehnoloģijas. | - Uzlabojiet griešanas precizitāti un samaziniet materiālu izšķērdēšanu. |
- Ieviest lāzergriešanas tehnoloģiju, kas piemērota augstas cietības materiālu plāksnēm. | - Uzlabot ražošanas efektivitāti un samazināt manuālās kļūdas. | |
- Palielināt iekārtu automatizāciju automātiskai uzraudzībai un regulēšanai. | ||
Precīza parametru kontrole | - Precīzi pielāgojiet parametrus, piemēram, griešanas dziļumu, ātrumu, instrumenta veidu un dzesēšanas metodes. | - Nodrošināt matricas integritāti un elektrisko veiktspēju. |
- Pielāgojiet parametrus, pamatojoties uz vafeļu materiālu, biezumu un struktūru. | - Palielināt ražas apjomus, samazināt materiālu atkritumus un samazināt ražošanas izmaksas. | |
Stratēģiskā nozīme | - Nepārtraukti izpētīt jaunas tehnoloģiskās iespējas, optimizēt procesus un uzlabot iekārtu iespējas, lai apmierinātu tirgus pieprasījumu. | - Uzlabot mikroshēmu ražošanas ražību un veiktspēju, atbalstot jaunu materiālu un modernu mikroshēmu dizainu izstrādi. |
1.2 Vafeļu griešanas kubiņos nozīme
Plākšņu sagriešanai ir izšķiroša nozīme pusvadītāju ražošanas procesā, tieši ietekmējot nākamos posmus, kā arī gatavā produkta kvalitāti un veiktspēju. Tās nozīmi var aprakstīt šādi:
Pirmkārt, griešanas precizitāte un konsekvence ir būtiska, lai nodrošinātu mikroshēmas ražu un uzticamību. Ražošanas laikā vafeles tiek pakļautas vairākiem apstrādes posmiem, lai izveidotu daudzas sarežģītas shēmu struktūras, kas precīzi jāsadala atsevišķās mikroshēmās (kasetelēs). Ja griešanas procesā rodas būtiskas izlīdzināšanas vai griešanas kļūdas, shēmas var tikt bojātas, ietekmējot mikroshēmas funkcionalitāti un uzticamību. Tāpēc augstas precizitātes griešanas tehnoloģija ne tikai nodrošina katras mikroshēmas integritāti, bet arī novērš iekšējo shēmu bojājumus, uzlabojot kopējo ražas līmeni.
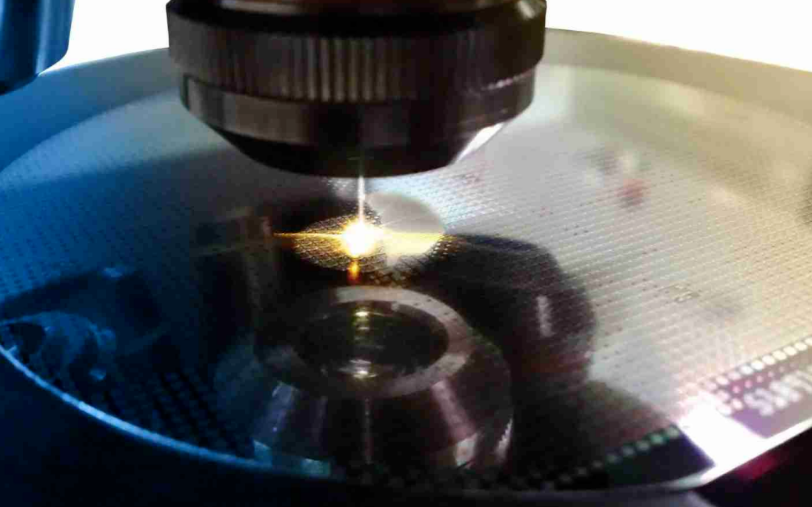
Otrkārt, vafeļu griešanai kubiņos ir būtiska ietekme uz ražošanas efektivitāti un izmaksu kontroli. Tā kā tas ir izšķirošs ražošanas procesa posms, tā efektivitāte tieši ietekmē nākamo posmu progresu. Optimizējot griešanas procesu, palielinot automatizācijas līmeni un uzlabojot griešanas ātrumu, kopējo ražošanas efektivitāti var ievērojami uzlabot.
No otras puses, materiālu zudumi griešanas laikā ir kritisks faktors izmaksu pārvaldībā. Izmantojot progresīvas griešanas tehnoloģijas, ne tikai tiek samazināti nevajadzīgi materiālu zudumi griešanas procesā, bet arī palielinās plākšņu izmantošanas apjoms, tādējādi samazinot ražošanas izmaksas.
Attīstoties pusvadītāju tehnoloģijai, plākšņu diametri turpina palielināties, un attiecīgi palielinās shēmu blīvums, izvirzot augstākas prasības sadalīšanas tehnoloģijai. Lielākām plāksnēm ir nepieciešama precīzāka griešanas ceļu kontrole, īpaši augsta blīvuma shēmu zonās, kur pat nelielas novirzes var izraisīt vairāku mikroshēmu defektus. Turklāt lielākām plāksnēm ir nepieciešams vairāk griešanas līniju un sarežģītāki procesa soļi, kas prasa turpmākus uzlabojumus sadalīšanas tehnoloģiju precizitātē, konsekvencē un efektivitātē, lai risinātu šīs problēmas.
1.3 Vafeļu griešanas process
Vafeļu griešanas process ietver visus soļus no sagatavošanas fāzes līdz galīgajai kvalitātes pārbaudei, un katrs posms ir kritiski svarīgs, lai nodrošinātu sagriezto mikroshēmu kvalitāti un veiktspēju. Zemāk ir sniegts detalizēts katras fāzes skaidrojums.
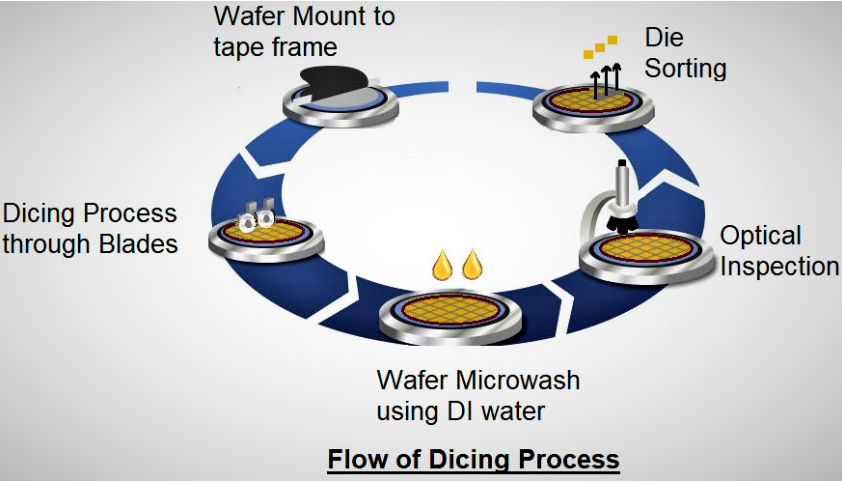
Fāze | Detalizēts apraksts |
Sagatavošanās fāze | -Vafeļu tīrīšanaIzmantojiet augstas tīrības ūdeni un specializētus tīrīšanas līdzekļus apvienojumā ar ultraskaņas vai mehānisko beršanu, lai noņemtu piemaisījumus, daļiņas un piesārņotājus, nodrošinot tīru virsmu. -Precīza pozicionēšanaIzmantojiet augstas precizitātes aprīkojumu, lai nodrošinātu, ka vafele tiek precīzi sadalīta pa paredzētajām griešanas trajektorijām. -Vafeļu fiksācijaNostipriniet plāksni uz lentes rāmja, lai griešanas laikā saglabātu stabilitāti, novēršot bojājumus vibrācijas vai kustības dēļ. |
Griešanas fāze | -Asmens griešana kubiņosFiziskai griešanai izmantojiet ātrgaitas rotējošus dimanta pārklājuma asmeņus, kas ir piemēroti silikona bāzes materiāliem un ir rentabli. -Lāzera griešana kubiņosIzmantojiet augstas enerģijas lāzera starus bezkontakta griešanai, kas ir ideāli piemērots trausliem vai augstas cietības materiāliem, piemēram, gallija nitrīdam, nodrošinot augstāku precizitāti un mazākus materiāla zudumus. -Jaunās tehnoloģijasIeviest lāzera un plazmas griešanas tehnoloģijas, lai vēl vairāk uzlabotu efektivitāti un precizitāti, vienlaikus samazinot karstuma ietekmētās zonas. |
Tīrīšanas fāze | - Izmantojiet dejonizētu ūdeni (DI ūdeni) un specializētus tīrīšanas līdzekļus apvienojumā ar ultraskaņas vai aerosola tīrīšanu, lai noņemtu griešanas laikā radušos gružus un putekļus, novēršot, ka atlikumi ietekmē turpmākos procesus vai mikroshēmas elektrisko veiktspēju. - Augstas tīrības pakāpes dejonizētais ūdens novērš jaunu piesārņotāju iekļūšanu, nodrošinot tīru vafeļu vidi. |
Pārbaudes fāze | -Optiskā pārbaudeIzmantojiet optiskās noteikšanas sistēmas apvienojumā ar mākslīgā intelekta algoritmiem, lai ātri identificētu defektus, nodrošinot, ka sagrieztajās skaidās nav plaisu vai šķembu, uzlabojot pārbaudes efektivitāti un samazinot cilvēciskās kļūdas. -Izmēru mērīšanaPārliecinieties, vai mikroshēmas izmēri atbilst konstrukcijas specifikācijām. -Elektriskās veiktspējas pārbaudeNodrošināt, lai kritisko mikroshēmu elektriskā veiktspēja atbilstu standartiem, garantējot uzticamību turpmākajos lietojumos. |
Šķirošanas fāze | - Izmantojiet robotizētas rokas vai vakuuma piesūcekņus, lai atdalītu kvalificētas mikroshēmas no lentes rāmja un automātiski šķirotu tās pēc veiktspējas, nodrošinot ražošanas efektivitāti un elastību, vienlaikus uzlabojot precizitāti. |
Plākšņu griešanas process ietver plākšņu tīrīšanu, pozicionēšanu, griešanu, tīrīšanu, pārbaudi un šķirošanu, un katrs solis ir kritiski svarīgs. Attīstoties automatizācijai, lāzergriešanai un mākslīgā intelekta pārbaudes tehnoloģijām, mūsdienu plākšņu griešanas sistēmas var sasniegt lielāku precizitāti, ātrumu un mazākus materiālu zudumus. Nākotnē jaunas griešanas tehnoloģijas, piemēram, lāzers un plazma, pakāpeniski aizstās tradicionālo griešanu ar asmeni, lai apmierinātu arvien sarežģītāku mikroshēmu konstrukciju vajadzības, vēl vairāk veicinot pusvadītāju ražošanas procesu attīstību.
Vafeļu griešanas tehnoloģija un tās principi
Attēlā redzamās trīs izplatītas vafeļu griešanas tehnoloģijas:Asmens griešana kubiņos,Lāzera griešana kubiņosunPlazmas kubiņos sagriešanaZemāk ir sniegta detalizēta šo trīs metožu analīze un papildu skaidrojums:
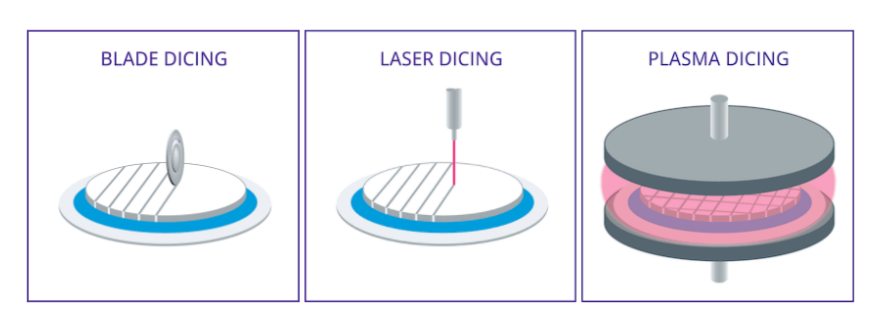
Pusvadītāju ražošanā plākšņu griešana ir izšķirošs solis, kurā jāizvēlas atbilstoša griešanas metode, pamatojoties uz plāksnītes biezumu. Pirmais solis ir noteikt plāksnītes biezumu. Ja plāksnītes biezums pārsniedz 100 mikronus, kā griešanas metodi var izvēlēties asmeņu griešanu. Ja asmeņu griešana nav piemērota, var izmantot lūzuma griešanu, kas ietver gan griešanas ar skrejceļu, gan asmeņu griešanu.
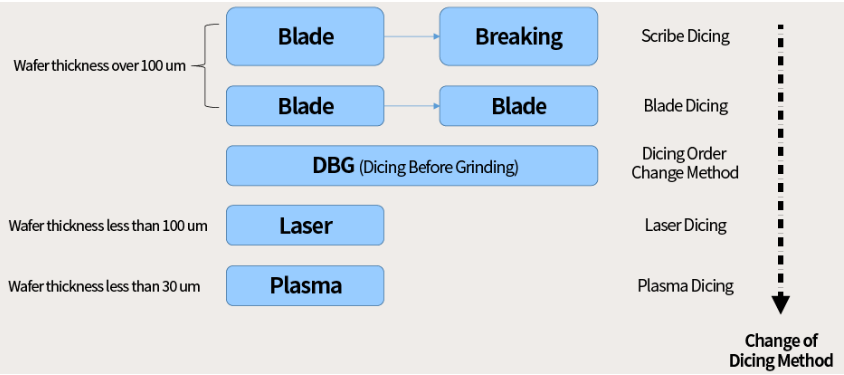
Ja vafeļu biezums ir no 30 līdz 100 mikroniem, ieteicama DBG (Dice Before Grinding — kubiņu griešana pirms slīpēšanas) metode. Šajā gadījumā labāko rezultātu sasniegšanai var izvēlēties griešanu ar aizspiedņiem, griešanu ar asmeni vai griešanas secības pielāgošanu pēc nepieciešamības.
Ultraplānām plāksnēm, kuru biezums ir mazāks par 30 mikroniem, lāzergriešana kļūst par vēlamo metodi, jo tā spēj precīzi sagriezt plānas plāksnītes, neradot pārmērīgus bojājumus. Ja lāzergriešana nevar izpildīt īpašas prasības, kā alternatīvu var izmantot plazmas griešanu. Šī blokshēma sniedz skaidru lēmumu pieņemšanas ceļu, lai nodrošinātu, ka dažādos biezuma apstākļos tiek izvēlēta vispiemērotākā plāksnīšu griešanas tehnoloģija.
2.1 Mehāniskā griešanas tehnoloģija
Mehāniskā griešanas tehnoloģija ir tradicionālā metode vafeļu sagriešanā. Galvenais princips ir izmantot ātrgaitas rotējošu dimanta slīpripu kā griezējinstrumentu vafeļu griešanai. Galvenā iekārta ietver gaisa gultņu vārpstu, kas darbina dimanta slīpripas instrumentu ar lielu ātrumu, lai veiktu precīzu griešanu vai rievojumu veidošanu pa iepriekš noteiktu griešanas trajektoriju. Šī tehnoloģija tiek plaši izmantota rūpniecībā, pateicoties tās zemajām izmaksām, augstajai efektivitātei un plašajam pielietojumam.
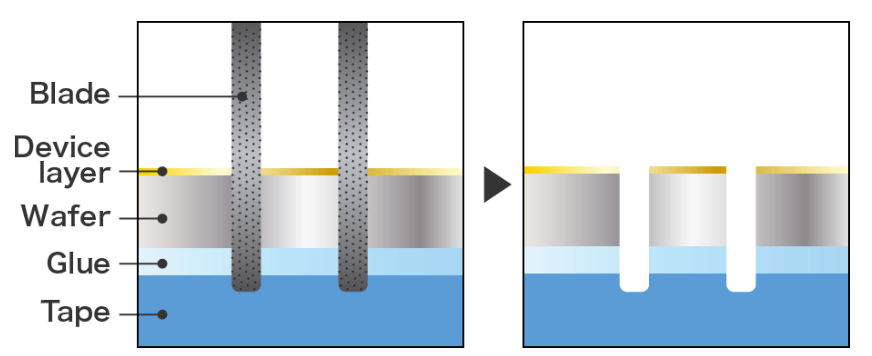
Priekšrocības
Dimanta slīpripu instrumentu augstā cietība un nodilumizturība ļauj mehāniskās griešanas tehnoloģijai pielāgoties dažādu vafeļu materiālu griešanas vajadzībām, neatkarīgi no tā, vai tie ir tradicionāli uz silīcija bāzes veidoti materiāli vai jaunāki salikto pusvadītāju materiāli. Tās darbība ir vienkārša, ar salīdzinoši zemām tehniskajām prasībām, kas vēl vairāk veicina tās popularitāti masveida ražošanā. Turklāt, salīdzinot ar citām griešanas metodēm, piemēram, lāzergriešanu, mehāniskajai griešanai ir labāk kontrolējamas izmaksas, padarot to piemērotu liela apjoma ražošanas vajadzībām.
Ierobežojumi
Neskatoties uz daudzajām priekšrocībām, mehāniskajai griešanas tehnoloģijai ir arī ierobežojumi. Pirmkārt, fiziskā kontakta starp instrumentu un plāksni dēļ griešanas precizitāte ir relatīvi ierobežota, kas bieži vien noved pie izmēru novirzēm, kas var ietekmēt sekojošās mikroshēmu iepakošanas un testēšanas precizitāti. Otrkārt, mehāniskās griešanas procesā var viegli rasties tādi defekti kā šķembas un plaisas, kas ne tikai ietekmē ražas koeficientu, bet arī var negatīvi ietekmēt mikroshēmu uzticamību un kalpošanas laiku. Mehāniskās spriedzes radītie bojājumi ir īpaši kaitīgi augsta blīvuma mikroshēmu ražošanā, īpaši griežot trauslus materiālus, kur šīs problēmas ir izteiktākas.
Tehnoloģiskie uzlabojumi
Lai pārvarētu šos ierobežojumus, pētnieki nepārtraukti optimizē mehāniskās griešanas procesu. Galvenie uzlabojumi ietver slīpripu konstrukcijas un materiālu izvēles uzlabošanu, lai uzlabotu griešanas precizitāti un izturību. Turklāt griešanas iekārtu konstrukcijas dizaina un vadības sistēmu optimizācija ir vēl vairāk uzlabojusi griešanas procesa stabilitāti un automatizāciju. Šie uzlabojumi samazina cilvēku darbību radītās kļūdas un uzlabo griezumu konsekvenci. Uzlabotu pārbaudes un kvalitātes kontroles tehnoloģiju ieviešana anomāliju uzraudzībai reāllaikā griešanas procesa laikā ir arī ievērojami uzlabojusi griešanas uzticamību un ražību.
Nākotnes attīstība un jaunās tehnoloģijas
Lai gan mehāniskās griešanas tehnoloģija joprojām ieņem nozīmīgu vietu plākšņu griešanā, jaunās griešanas tehnoloģijas strauji attīstās, attīstoties pusvadītāju procesiem. Piemēram, termiskās lāzergriešanas tehnoloģijas pielietošana sniedz jaunus risinājumus precizitātes un defektu problēmām mehāniskajā griešanas procesā. Šī bezkontakta griešanas metode samazina fizisko spriegumu uz plāksni, ievērojami samazinot šķembu un plaisāšanas biežumu, īpaši griežot trauslākus materiālus. Nākotnē mehāniskās griešanas tehnoloģijas integrācija ar jaunajām griešanas metodēm nodrošinās pusvadītāju ražošanai vairāk iespēju un elastības, vēl vairāk uzlabojot ražošanas efektivitāti un mikroshēmu kvalitāti.
Noslēgumā jāsaka, ka, lai gan mehāniskās griešanas tehnoloģijai ir zināmi trūkumi, nepārtraukti tehnoloģiskie uzlabojumi un to integrācija ar jaunām griešanas metodēm ļauj tai joprojām ieņemt svarīgu lomu pusvadītāju ražošanā un saglabāt tās konkurētspēju nākotnes procesos.
2.2 Lāzergriešanas tehnoloģija
Lāzergriešanas tehnoloģija kā jauna metode plākšņu griešanā ir pakāpeniski ieguvusi plašu uzmanību pusvadītāju nozarē, pateicoties tās augstajai precizitātei, mehānisku kontakta bojājumu trūkumam un ātrajām griešanas iespējām. Šī tehnoloģija izmanto lāzera stara augsto enerģijas blīvumu un fokusēšanas spēju, lai izveidotu nelielu termiski ietekmētu zonu uz plāksnītes materiāla virsmas. Kad lāzera stars tiek pielikts plāksnei, radītais termiskais spriegums izraisa materiāla lūzumu norādītajā vietā, panākot precīzu griešanu.
Lāzergriešanas tehnoloģijas priekšrocības
• Augsta precizitāteLāzera stara precīzās pozicionēšanas spējas ļauj sasniegt mikronu vai pat nanometru līmeņa griešanas precizitāti, kas atbilst mūsdienu augstas precizitātes, augsta blīvuma integrēto shēmu ražošanas prasībām.
• Nav mehāniska kontaktaLāzergriešana ļauj izvairīties no fiziska kontakta ar vafeli, novēršot mehāniskās griešanas laikā bieži sastopamas problēmas, piemēram, šķembēšanu un plaisāšanu, ievērojami uzlabojot čipu ražas apjomu un uzticamību.
• Ātrs griešanas ātrumsLāzergriešanas lielais ātrums veicina ražošanas efektivitātes pieaugumu, padarot to īpaši piemērotu liela mēroga, ātrgaitas ražošanas scenārijiem.
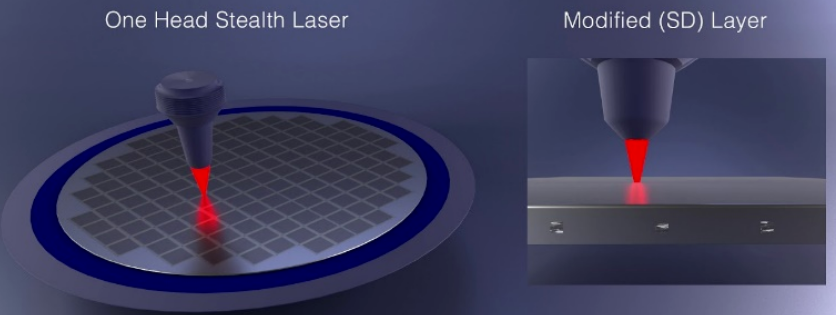
Sastaptie izaicinājumi
• Augstas aprīkojuma izmaksasSākotnējās investīcijas lāzergriešanas iekārtām ir lielas, kas rada ekonomisku spiedienu, īpaši maziem un vidējiem ražošanas uzņēmumiem.
• Sarežģīta procesu kontroleLāzergriešanai nepieciešama precīza vairāku parametru kontrole, tostarp enerģijas blīvums, fokusa pozīcija un griešanas ātrums, kas padara procesu sarežģītu.
• Karstuma skartās zonas problēmasLai gan lāzergriešanas bezkontakta daba samazina mehāniskos bojājumus, termiskā spriedze, ko rada termiski ietekmētā zona (HAZ), var negatīvi ietekmēt vafeļu materiāla īpašības. Lai mazinātu šo ietekmi, ir nepieciešama turpmāka procesa optimizācija.
Tehnoloģiju uzlabošanas virzieni
Lai risinātu šīs problēmas, pētnieki koncentrējas uz iekārtu izmaksu samazināšanu, griešanas efektivitātes uzlabošanu un procesa plūsmas optimizēšanu.
• Efektīvi lāzeri un optiskās sistēmasIzstrādājot efektīvākus lāzerus un uzlabotas optiskās sistēmas, ir iespējams samazināt iekārtu izmaksas, vienlaikus uzlabojot griešanas precizitāti un ātrumu.
• Procesa parametru optimizēšanaTiek veikti padziļināti pētījumi par lāzeru un plākšņu materiālu mijiedarbību, lai uzlabotu procesus, kas samazina karstuma ietekmēto zonu, tādējādi uzlabojot griešanas kvalitāti.
• Inteliģentas vadības sistēmasInteliģento vadības tehnoloģiju izstrādes mērķis ir automatizēt un optimizēt lāzergriešanas procesu, uzlabojot tā stabilitāti un konsekvenci.
Lāzergriešanas tehnoloģija ir īpaši efektīva īpaši plānu plākšņu un augstas precizitātes griešanas scenārijos. Palielinoties plākšņu izmēriem un shēmu blīvumam, tradicionālajām mehāniskajām griešanas metodēm ir grūti apmierināt mūsdienu pusvadītāju ražošanas augstas precizitātes un augstas efektivitātes prasības. Pateicoties savām unikālajām priekšrocībām, lāzergriešana kļūst par vēlamo risinājumu šajās jomās.
Lai gan lāzergriešanas tehnoloģija joprojām saskaras ar tādiem izaicinājumiem kā augstas iekārtu izmaksas un procesa sarežģītība, tās unikālās priekšrocības augstā precizitātē un bezkontakta bojājumu novēršanā padara to par svarīgu attīstības virzienu pusvadītāju ražošanā. Lāzertehnoloģijām un inteliģentām vadības sistēmām turpinot attīstīties, paredzams, ka lāzergriešana vēl vairāk uzlabos vafeļu griešanas efektivitāti un kvalitāti, veicinot pusvadītāju nozares nepārtrauktu attīstību.
2.3 Plazmas griešanas tehnoloģija
Plazmas griešanas tehnoloģija kā jauna vafeļu griešanas metode pēdējos gados ir ieguvusi ievērojamu uzmanību. Šī tehnoloģija izmanto augstas enerģijas plazmas starus, lai precīzi sagrieztu vafeļus, kontrolējot plazmas stara enerģiju, ātrumu un griešanas ceļu, tādējādi panākot optimālus griešanas rezultātus.
Darbības princips un priekšrocības
Plazmas griešanas process balstās uz iekārtas ģenerētu augstas temperatūras un enerģijas plazmas staru kūli. Šis stars ļoti īsā laikā var uzsildīt plāksnītes materiālu līdz tā kušanas vai iztvaikošanas temperatūrai, nodrošinot ātru griešanu. Salīdzinot ar tradicionālo mehānisko vai lāzergriešanu, plazmas griešana ir ātrāka un rada mazāku karstuma ietekmēto zonu, efektīvi samazinot plaisu un bojājumu rašanos griešanas laikā.
Praktiskos pielietojumos plazmas griešanas tehnoloģija ir īpaši piemērota sarežģītu formu plākšņu apstrādei. Tās augstas enerģijas, regulējamais plazmas stars var viegli un precīzi sagriezt neregulāras formas plāksnītes. Tāpēc mikroelektronikas ražošanā, īpaši augstas klases mikroshēmu pielāgotā un mazo partiju ražošanā, šī tehnoloģija ir ļoti daudzsološa plašai izmantošanai.
Izaicinājumi un ierobežojumi
Neskatoties uz daudzajām plazmas griešanas tehnoloģijas priekšrocībām, tai ir arī dažas grūtības.
• Sarežģīts processPlazmas griešanas process ir sarežģīts un prasa augstas precizitātes aprīkojumu un pieredzējušus operatorus, lai nodrošinātuprecizitāte un stabilitāte griešanas laikā.
• Vides kontrole un drošībaPlazmas stara augstās temperatūras un enerģijas dēļ ir nepieciešami stingri vides kontroles un drošības pasākumi, kas palielina ieviešanas sarežģītību un izmaksas.
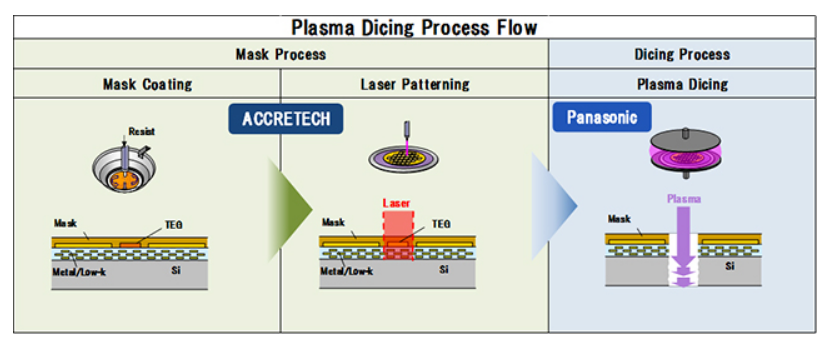
Nākotnes attīstības virzieni
Līdz ar tehnoloģiju attīstību paredzams, ka pakāpeniski tiks pārvarētas ar plazmas griešanu saistītās problēmas. Izstrādājot viedākas un stabilākas griešanas iekārtas, var samazināt atkarību no manuālām darbībām, tādējādi uzlabojot ražošanas efektivitāti. Vienlaikus procesa parametru un griešanas vides optimizēšana palīdzēs samazināt drošības riskus un ekspluatācijas izmaksas.
Pusvadītāju nozarē inovācijas plākšņu griešanas un sadalīšanas tehnoloģijās ir izšķiroši svarīgas nozares attīstības veicināšanai. Plazmas griešanas tehnoloģija ar savu augsto precizitāti, efektivitāti un spēju apstrādāt sarežģītas plākšņu formas ir kļuvusi par nozīmīgu jaunu spēlētāju šajā jomā. Lai gan joprojām pastāv dažas problēmas, tās tiks pakāpeniski risinātas, turpinot tehnoloģiskās inovācijas, radot vairāk iespēju pusvadītāju ražošanā.
Plazmas griešanas tehnoloģijas pielietojuma perspektīvas ir plašas, un paredzams, ka nākotnē tai būs vēl svarīgāka loma pusvadītāju ražošanā. Pateicoties nepārtrauktai tehnoloģiskai inovācijai un optimizācijai, plazmas griešana ne tikai risinās esošās problēmas, bet arī kļūs par spēcīgu pusvadītāju nozares izaugsmes virzītājspēku.
2.4 Griešanas kvalitāte un ietekmējošie faktori
Plākšņu griešanas kvalitāte ir kritiski svarīga turpmākajai mikroshēmu iepakošanai, testēšanai, kā arī gala produkta kopējai veiktspējai un uzticamībai. Bieži sastopamas problēmas griešanas laikā ir plaisas, šķembas un griešanas novirzes. Šīs problēmas ietekmē vairāki faktori, kas darbojas kopā.
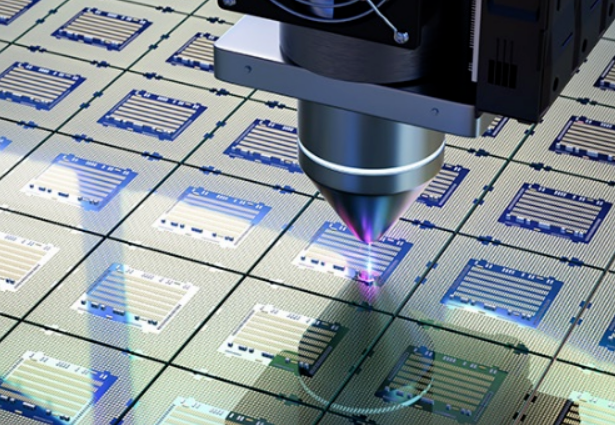
Kategorija | Saturs | Ietekme |
Procesa parametri | Griešanas ātrums, padeves ātrums un griešanas dziļums tieši ietekmē griešanas procesa stabilitāti un precizitāti. Nepareizi iestatījumi var izraisīt sprieguma koncentrāciju un pārmērīgu karstuma ietekmēto zonu, kā rezultātā rodas plaisas un šķembas. Parametru atbilstoša pielāgošana, pamatojoties uz plātnes materiālu, biezumu un griešanas prasībām, ir būtiska, lai sasniegtu vēlamos griešanas rezultātus. | Pareizie procesa parametri nodrošina precīzu griešanu un samazina tādu defektu kā plaisu un šķembu risku. |
Iekārtu un materiālu faktori | -Asmens kvalitāteAsmens materiāls, cietība un nodilumizturība ietekmē griešanas procesa vienmērīgumu un grieztās virsmas līdzenumu. Sliktas kvalitātes asmeņi palielina berzi un termisko spriegumu, kas var izraisīt plaisas vai šķembas. Pareiza asmens materiāla izvēle ir ļoti svarīga. -Dzesēšanas šķidruma veiktspējaDzesēšanas šķidrumi palīdz samazināt griešanas temperatūru, minimizēt berzi un likvidēt gružus. Neefektīvs dzesēšanas šķidrums var izraisīt augstu temperatūru un gružu uzkrāšanos, ietekmējot griešanas kvalitāti un efektivitāti. Ir ļoti svarīgi izvēlēties efektīvus un videi draudzīgus dzesēšanas šķidrumus. | Asmens kvalitāte ietekmē griešanas precizitāti un gludumu. Neefektīvs dzesēšanas šķidrums var izraisīt sliktu griešanas kvalitāti un efektivitāti, kas uzsver nepieciešamību pēc optimālas dzesēšanas šķidruma izmantošanas. |
Procesa kontrole un kvalitātes pārbaude | -Procesa kontroleGalveno griešanas parametru uzraudzība un pielāgošana reāllaikā, lai nodrošinātu griešanas procesa stabilitāti un konsekvenci. -Kvalitātes pārbaudePēcgriešanas izskata pārbaudes, izmēru mērījumi un elektriskās veiktspējas pārbaude palīdz nekavējoties identificēt un risināt kvalitātes problēmas, uzlabojot griešanas precizitāti un konsekvenci. | Pareiza procesa kontrole un kvalitātes pārbaude palīdz nodrošināt nemainīgus, augstas kvalitātes griešanas rezultātus un potenciālo problēmu agrīnu atklāšanu. |

Griešanas kvalitātes uzlabošana
Griešanas kvalitātes uzlabošanai nepieciešama visaptveroša pieeja, kas ņem vērā procesa parametrus, iekārtu un materiālu izvēli, procesa kontroli un pārbaudi. Pastāvīgi pilnveidojot griešanas tehnoloģijas un optimizējot procesa metodes, var vēl vairāk uzlabot vafeļu griešanas precizitāti un stabilitāti, nodrošinot uzticamāku tehnisko atbalstu pusvadītāju ražošanas nozarei.
#03 Pēcapstrāde un testēšana
3.1 Tīrīšana un žāvēšana
Tīrīšanas un žāvēšanas posmi pēc vafeļu griešanas ir ļoti svarīgi, lai nodrošinātu mikroshēmas kvalitāti un turpmāko procesu vienmērīgu norisi. Šajā posmā ir svarīgi rūpīgi noņemt silīcija atliekas, dzesēšanas šķidruma atliekas un citus griešanas laikā radušos piesārņotājus. Tikpat svarīgi ir nodrošināt, lai tīrīšanas procesa laikā mikroshēmas netiktu bojātas, un pēc žāvēšanas pārliecināties, ka uz mikroshēmas virsmas nepaliek mitrums, lai novērstu tādas problēmas kā korozija vai elektrostatiskā izlāde.
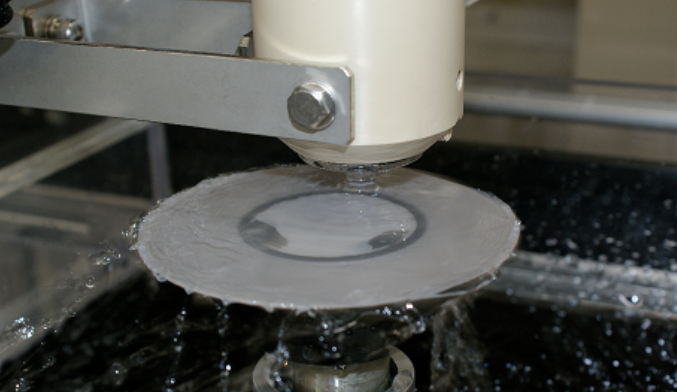
Pēcapstrāde: tīrīšanas un žāvēšanas process
Procesa solis | Saturs | Ietekme |
Tīrīšanas process | -MetodeTīrīšanai izmantojiet specializētus tīrīšanas līdzekļus un tīru ūdeni, kā arī ultraskaņas vai mehāniskās tīrīšanas metodes. | Nodrošina rūpīgu piesārņotāju noņemšanu un novērš skaidu bojājumus tīrīšanas laikā. |
-Tīrīšanas līdzekļa izvēleIzvēlieties, pamatojoties uz vafeļu materiālu un piesārņojuma veidu, lai nodrošinātu efektīvu tīrīšanu, nebojājot mikroshēmu. | Pareiza tīrīšanas līdzekļa izvēle ir efektīvas tīrīšanas un šķembu aizsardzības atslēga. | |
-Parametru kontroleStingri kontrolējiet tīrīšanas temperatūru, laiku un tīrīšanas šķīduma koncentrāciju, lai novērstu nepareizas tīrīšanas izraisītas kvalitātes problēmas. | Vadības ierīces palīdz izvairīties no vafeļu bojājumiem vai piesārņotāju atstāšanas, nodrošinot nemainīgu kvalitāti. | |
Žāvēšanas process | -Tradicionālās metodesDabiskā gaisa žāvēšana un karstā gaisa žāvēšana, kurām ir zema efektivitāte un kuras var izraisīt statiskās elektrības uzkrāšanos. | Var izraisīt ilgāku žūšanas laiku un iespējamas statiskās elektrības problēmas. |
-Modernās tehnoloģijasIzmantojiet progresīvas tehnoloģijas, piemēram, vakuuma žāvēšanu un infrasarkano staru žāvēšanu, lai nodrošinātu, ka skaidas ātri izžūst un izvairās no kaitīgas ietekmes. | Ātrāks un efektīvāks žāvēšanas process, kas samazina statiskās izlādes vai ar mitrumu saistītu problēmu risku. | |
Iekārtu izvēle un apkope | -Aprīkojuma izvēleAugstas veiktspējas tīrīšanas un žāvēšanas iekārtas uzlabo apstrādes efektivitāti un precīzi kontrolē iespējamās problēmas apstrādes laikā. | Augstas kvalitātes iekārtas nodrošina labāku apstrādi un samazina kļūdu iespējamību tīrīšanas un žāvēšanas laikā. |
-Iekārtu apkopeRegulāra iekārtu pārbaude un apkope nodrošina to optimālu darba stāvokli, garantējot skaidu kvalitāti. | Pareiza apkope novērš iekārtu bojājumus, nodrošinot uzticamu un kvalitatīvu apstrādi. |
Pēcapgriešanas tīrīšana un žāvēšana
Tīrīšanas un žāvēšanas posmi pēc vafeļu griešanas ir sarežģīti un delikāti procesi, kuros rūpīgi jāņem vērā vairāki faktori, lai nodrošinātu galīgo apstrādes rezultātu. Izmantojot zinātniskas metodes un stingras procedūras, ir iespējams nodrošināt, ka katra mikroshēma nonāk nākamajās iepakošanas un testēšanas stadijās optimālā stāvoklī.
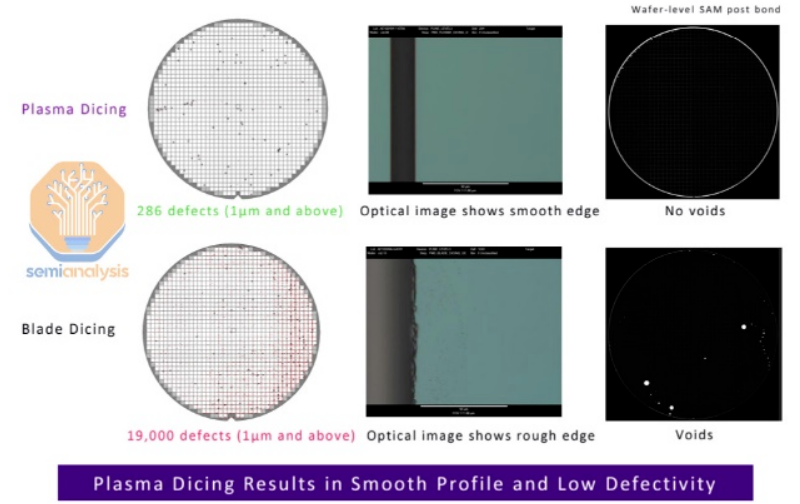
Pēcgriešanas pārbaude un testēšana
Solis | Saturs | Ietekme |
Pārbaudes solis | 1.Vizuāla pārbaudeIzmantojiet vizuālas vai automatizētas pārbaudes iekārtas, lai pārbaudītu, vai uz mikroshēmas virsmas nav redzamu defektu, piemēram, plaisu, šķembu vai piesārņojuma. Ātri identificējiet fiziski bojātas mikroshēmas, lai izvairītos no atkritumiem. | Palīdz identificēt un novērst bojātas skaidas procesa sākumā, samazinot materiālu zudumus. |
2.Izmēra mērīšanaIzmantojiet precīzas mērīšanas ierīces, lai precīzi izmērītu skaidu izmērus, nodrošinot, ka griešanas izmērs atbilst konstrukcijas specifikācijām, un novēršot veiktspējas problēmas vai iepakošanas grūtības. | Nodrošina, ka mikroshēmas atbilst noteiktajiem izmēra ierobežojumiem, novēršot veiktspējas pasliktināšanos vai montāžas problēmas. | |
3.Elektriskās veiktspējas pārbaudeNovērtējiet galvenos elektriskos parametrus, piemēram, pretestību, kapacitāti un induktivitāti, lai identificētu neatbilstošas mikroshēmas un nodrošinātu, ka nākamajā posmā nonāk tikai veiktspējai kvalificētas mikroshēmas. | Nodrošina, ka procesā tiek virzītas tikai funkcionālas un veiktspējas ziņā pārbaudītas mikroshēmas, tādējādi samazinot kļūmju risku vēlākos posmos. | |
Testēšanas solis | 1.Funkcionālā testēšanaPārbaudiet, vai mikroshēmas pamatfunkcijas darbojas, kā paredzēts, identificējot un novēršot mikroshēmas ar funkcionālām novirzēm. | Nodrošina, ka mikroshēmas atbilst pamata darbības prasībām, pirms tās pāriet uz vēlākiem posmiem. |
2.Uzticamības pārbaudeNovērtējiet mikroshēmas veiktspējas stabilitāti ilgstošas lietošanas vai skarbos apstākļos, parasti ietverot novecošanu augstā temperatūrā, testēšanu zemā temperatūrā un mitruma testēšanu, lai simulētu reālus ekstremālus apstākļus. | Nodrošina mikroshēmu drošu darbību dažādos vides apstākļos, uzlabojot produkta ilgmūžību un stabilitāti. | |
3.Saderības pārbaudePārliecinieties, vai mikroshēma darbojas pareizi ar citiem komponentiem vai sistēmām, nodrošinot, ka nav kļūmju vai veiktspējas pasliktināšanās nesaderības dēļ. | Nodrošina vienmērīgu darbību reālās pasaules lietojumprogrammās, novēršot saderības problēmas. |
3.3 Iepakošana un uzglabāšana
Pēc vafeļu griešanas mikroshēmas ir svarīgs pusvadītāju ražošanas procesa rezultāts, un to iepakošanas un uzglabāšanas posmi ir tikpat svarīgi. Pareizi iepakošanas un uzglabāšanas pasākumi ir būtiski ne tikai mikroshēmu drošības un stabilitātes nodrošināšanai transportēšanas un uzglabāšanas laikā, bet arī stingra atbalsta nodrošināšanai turpmākajos ražošanas, testēšanas un iepakošanas posmos.
Pārbaudes un testēšanas posmu kopsavilkums:
Mikroshēmu pārbaudes un testēšanas posmi pēc vafeļu griešanas aptver virkni aspektu, tostarp vizuālu pārbaudi, izmēru mērīšanu, elektriskās veiktspējas testēšanu, funkcionālo testēšanu, uzticamības testēšanu un saderības testēšanu. Šie posmi ir savstarpēji saistīti un papildinoši, veidojot stabilu barjeru produkta kvalitātes un uzticamības nodrošināšanai. Izmantojot stingras pārbaudes un testēšanas procedūras, potenciālās problēmas var identificēt un nekavējoties atrisināt, nodrošinot, ka gala produkts atbilst klientu prasībām un cerībām.
Aspekts | Saturs |
Iepakojuma pasākumi | 1.AntistatisksIepakojuma materiāliem jābūt ar izcilām antistatiskām īpašībām, lai novērstu statiskās elektrības radītus ierīču bojājumus vai to darbības traucējumus. |
2.MitrumizturīgsIepakojuma materiāliem jābūt ar labu mitrumizturību, lai novērstu mitruma izraisītu koroziju un elektriskās veiktspējas pasliktināšanos. | |
3.TriecienizturīgsIepakojuma materiāliem jānodrošina efektīva triecienu absorbcija, lai aizsargātu mikroshēmas no vibrācijas un triecieniem transportēšanas laikā. | |
Uzglabāšanas vide | 1.Mitruma kontroleStingri kontrolējiet mitrumu atbilstošā diapazonā, lai novērstu mitruma absorbciju un koroziju, ko izraisa pārmērīgs mitrums, vai statiskas problēmas, ko izraisa zems mitruma līmenis. |
2.TīrībaUzturēt tīru uzglabāšanas vidi, lai izvairītos no skaidu piesārņošanas ar putekļiem un piemaisījumiem. | |
3.Temperatūras kontroleIestatiet saprātīgu temperatūras diapazonu un uzturiet temperatūras stabilitāti, lai novērstu paātrinātu novecošanos pārmērīga karstuma vai kondensācijas problēmu dēļ, ko izraisa zema temperatūra. | |
Regulāra pārbaude | Regulāri pārbaudiet un novērtējiet uzglabātās mikroshēmas, izmantojot vizuālas pārbaudes, izmēru mērījumus un elektriskās veiktspējas testus, lai savlaicīgi identificētu un risinātu iespējamās problēmas. Pamatojoties uz uzglabāšanas laiku un apstākļiem, plānojiet mikroshēmu izmantošanu, lai nodrošinātu to optimālu stāvokli. |
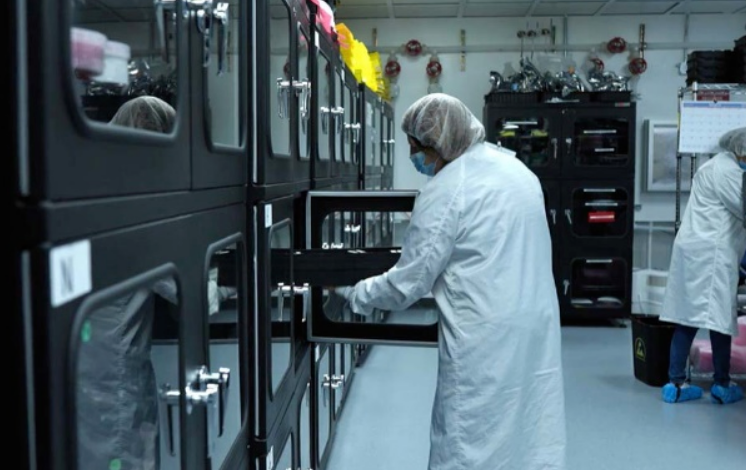
Mikroplaisu un bojājumu problēma vafeļu griešanas procesā ir ievērojams izaicinājums pusvadītāju ražošanā. Griešanas spriegums ir šīs parādības galvenais cēlonis, jo tas rada sīkas plaisas un bojājumus uz vafeļu virsmas, kā rezultātā palielinās ražošanas izmaksas un samazinās produkta kvalitāte.
Lai risinātu šo problēmu, ir ļoti svarīgi samazināt griešanas stresu un ieviest optimizētas griešanas metodes, instrumentus un apstākļus. Rūpīga uzmanība tādiem faktoriem kā asmens materiāls, griešanas ātrums, spiediens un dzesēšanas metodes var palīdzēt samazināt mikroplaisu veidošanos un uzlabot procesa kopējo ražu. Turklāt notiekošie pētījumi par progresīvākām griešanas tehnoloģijām, piemēram, lāzergriešanu, pēta veidus, kā vēl vairāk mazināt šīs problēmas.
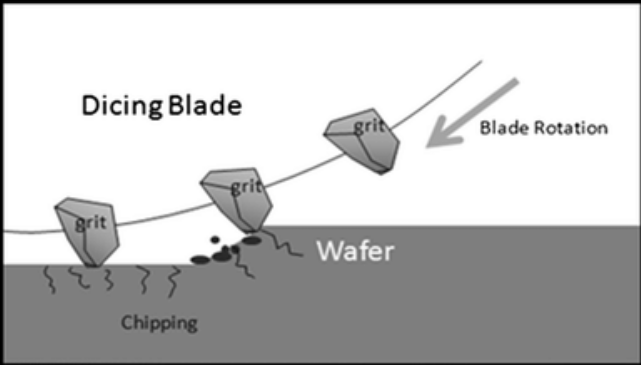
Kā trausls materiāls, vafeles ir pakļautas iekšējām strukturālām izmaiņām, ja tās tiek pakļautas mehāniskai, termiskai vai ķīmiskai slodzei, kā rezultātā veidojas mikroplaisas. Lai gan šīs plaisas var nebūt uzreiz pamanāmas, tās var paplašināties un radīt nopietnākus bojājumus ražošanas procesa gaitā. Šī problēma kļūst īpaši problemātiska turpmākajos iepakošanas un testēšanas posmos, kur temperatūras svārstības un papildu mehāniskais spriegums var izraisīt šo mikroplaisu pārvēršanos redzamās lūzumos, kas var izraisīt mikroshēmas atteici.
Lai mazinātu šo risku, ir svarīgi rūpīgi kontrolēt griešanas procesu, optimizējot tādus parametrus kā griešanas ātrums, spiediens un temperatūra. Izmantojot mazāk agresīvas griešanas metodes, piemēram, lāzergriešanu, var samazināt mehānisko spriegumu uz vafeles un līdz minimumam samazināt mikroplaisu veidošanos. Turklāt, ieviešot progresīvas pārbaudes metodes, piemēram, infrasarkano skenēšanu vai rentgena attēlveidošanu vafeles griešanas procesā, var palīdzēt atklāt šīs agrīnās stadijas plaisas, pirms tās rada turpmākus bojājumus.
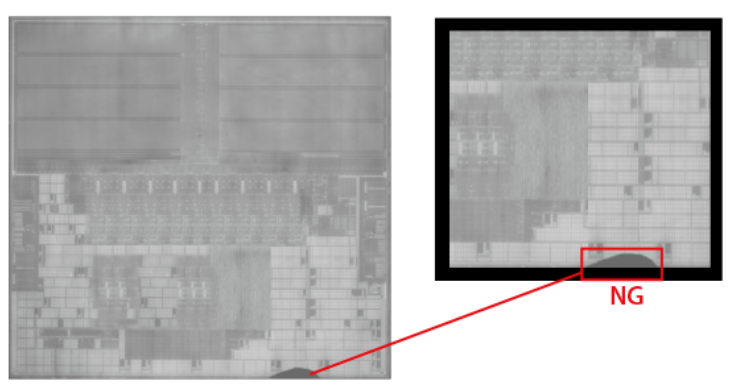
Bojājumi uz vafeles virsmas ir būtiska problēma sadalīšanas procesā, jo tie var tieši ietekmēt mikroshēmas veiktspēju un uzticamību. Šādus bojājumus var izraisīt nepareiza griezējinstrumentu lietošana, nepareizi griešanas parametri vai pašai vafelei raksturīgi materiālu defekti. Neatkarīgi no cēloņa, šie bojājumi var izraisīt ķēdes elektriskās pretestības vai kapacitātes izmaiņas, ietekmējot kopējo veiktspēju.
Lai risinātu šīs problēmas, tiek pētītas divas galvenās stratēģijas:
1. Griešanas instrumentu un parametru optimizācijaIzmantojot asākus asmeņus, regulējot griešanas ātrumu un mainot griešanas dziļumu, griešanas procesa laikā var samazināt sprieguma koncentrāciju, tādējādi samazinot bojājumu iespējamību.
2. Jaunu griešanas tehnoloģiju izpēteTādas progresīvas metodes kā lāzergriešana un plazmas griešana piedāvā uzlabotu precizitāti, vienlaikus potenciāli samazinot plāksnei nodarītos bojājumus. Šīs tehnoloģijas tiek pētītas, lai atrastu veidus, kā panākt augstu griešanas precizitāti, vienlaikus samazinot plāksnei radīto termisko un mehānisko spriegumu.
Termiskās ietekmes zona un tās ietekme uz veiktspēju
Termiskās griešanas procesos, piemēram, lāzera un plazmas griešanā, augsta temperatūra neizbēgami rada termiskās trieciena zonu uz vafeles virsmas. Šī zona, kur ir ievērojams temperatūras gradients, var mainīt materiāla īpašības, ietekmējot mikroshēmas galīgo veiktspēju.
Termiski skartās zonas (TAZ) ietekme:
Kristāla struktūras izmaiņasAugstās temperatūrās vafeļu materiāla atomi var pārkārtoties, izraisot kristāla struktūras deformācijas. Šīs deformācijas vājina materiālu, samazinot tā mehānisko izturību un stabilitāti, kas palielina mikroshēmas atteices risku lietošanas laikā.
Elektrisko īpašību izmaiņasAugsta temperatūra var mainīt nesēju koncentrāciju un mobilitāti pusvadītāju materiālos, ietekmējot mikroshēmas elektrovadītspēju un strāvas pārvades efektivitāti. Šīs izmaiņas var izraisīt mikroshēmas veiktspējas samazināšanos, potenciāli padarot to nepiemērotu paredzētajam mērķim.
Lai mazinātu šīs sekas, temperatūras kontrole griešanas laikā, griešanas parametru optimizēšana un tādu metožu kā dzesēšanas strūklu vai pēcapstrādes procedūru izpēte ir būtiskas stratēģijas, lai samazinātu termiskās ietekmes apmēru un saglabātu materiāla integritāti.
Kopumā gan mikroplaisas, gan termiskās trieciena zonas ir būtiskas problēmas vafeļu sadalīšanas tehnoloģijā. Lai uzlabotu pusvadītāju izstrādājumu kvalitāti un palielinātu to konkurētspēju tirgū, būs nepieciešami turpmāki pētījumi, kā arī tehnoloģiskie sasniegumi un kvalitātes kontroles pasākumi.
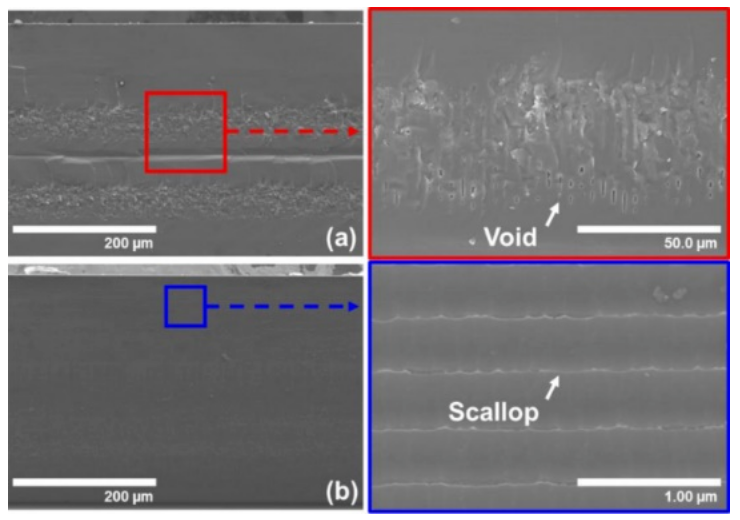
Pasākumi termiskās ietekmes zonas kontrolei:
Griešanas procesa parametru optimizēšanaGriešanas ātruma un jaudas samazināšana var efektīvi samazināt termiskās trieciena zonas (TAZ) izmēru. Tas palīdz kontrolēt griešanas procesā radītā siltuma daudzumu, kas tieši ietekmē vafeļu materiāla īpašības.
Uzlabotas dzesēšanas tehnoloģijasTādu tehnoloģiju kā šķidrā slāpekļa dzesēšanas un mikrofluidiskās dzesēšanas izmantošana var ievērojami ierobežot termiskā trieciena zonas diapazonu. Šīs dzesēšanas metodes palīdz efektīvāk izkliedēt siltumu, tādējādi saglabājot vafeļu materiāla īpašības un samazinot termiskos bojājumus.
Materiālu izvēlePētnieki pēta jaunus materiālus, piemēram, oglekļa nanocaurules un grafēnu, kuriem piemīt lieliska siltumvadītspēja un mehāniskā izturība. Šie materiāli var samazināt termiskās trieciena zonu, vienlaikus uzlabojot mikroshēmu kopējo veiktspēju.
Rezumējot, lai gan termiskās ietekmes zona ir neizbēgama termiskās griešanas tehnoloģiju sekas, to var efektīvi kontrolēt, optimizējot apstrādes metodes un izvēloties materiālus. Turpmākie pētījumi, visticamāk, būs vērsti uz termiskās griešanas procesu precizēšanu un automatizāciju, lai panāktu efektīvāku un precīzāku vafeļu sagriešanu.

Līdzsvara stratēģija:
Optimāla līdzsvara sasniegšana starp vafeļu ražu un ražošanas efektivitāti ir pastāvīgs izaicinājums vafeļu griešanas tehnoloģijā. Ražotājiem jāņem vērā vairāki faktori, piemēram, tirgus pieprasījums, ražošanas izmaksas un produkta kvalitāte, lai izstrādātu racionālu ražošanas stratēģiju un procesa parametrus. Vienlaikus ir jāievieš modernas griešanas iekārtas, jāuzlabo operatoru prasmes un jāuzlabo izejvielu kvalitātes kontrole, lai saglabātu vai pat uzlabotu ražu, vienlaikus palielinot ražošanas efektivitāti.
Nākotnes izaicinājumi un iespējas:
Attīstoties pusvadītāju tehnoloģijai, plākšņu griešana saskaras ar jauniem izaicinājumiem un iespējām. Samazinoties mikroshēmu izmēriem un palielinoties integrācijai, ievērojami pieaug prasības pēc griešanas precizitātes un kvalitātes. Vienlaikus jaunās tehnoloģijas sniedz jaunas idejas plākšņu griešanas metožu attīstībai. Ražotājiem ir jāseko līdzi tirgus dinamikai un tehnoloģiskajām tendencēm, nepārtraukti pielāgojot un optimizējot ražošanas stratēģijas un procesa parametrus, lai apmierinātu tirgus izmaiņas un tehnoloģiskās prasības.
Noslēgumā jāsaka, ka, integrējot tirgus pieprasījuma, ražošanas izmaksu un produktu kvalitātes apsvērumus, kā arī ieviešot modernu aprīkojumu un tehnoloģijas, uzlabojot operatoru prasmes un stiprinot izejvielu kontroli, ražotāji var panākt vislabāko līdzsvaru starp vafeļu ražu un ražošanas efektivitāti vafeļu sagriešanas laikā, tādējādi nodrošinot efektīvu un augstas kvalitātes pusvadītāju izstrādājumu ražošanu.
Nākotnes perspektīvas:
Līdz ar straujo tehnoloģiju attīstību pusvadītāju tehnoloģijas attīstās nepieredzētā tempā. Kā izšķirošs solis pusvadītāju ražošanā, plākšņu griešanas tehnoloģija ir gatava aizraujošām jaunām attīstības tendencēm. Raugoties nākotnē, tiek sagaidīts, ka plākšņu griešanas tehnoloģija sasniegs ievērojamus uzlabojumus precizitātes, efektivitātes un izmaksu ziņā, ienesot jaunu dzīvīgumu pusvadītāju nozares nepārtrauktajā izaugsmē.
Precizitātes palielināšana:
Tiecoties pēc lielākas precizitātes, vafeļu griešanas tehnoloģija nepārtraukti paplašinās esošo procesu robežas. Padziļināti izpētot griešanas procesa fizikālos un ķīmiskos mehānismus un precīzi kontrolējot griešanas parametrus, tiks sasniegti precīzāki griešanas rezultāti, lai apmierinātu arvien sarežģītākas shēmu projektēšanas prasības. Turklāt jaunu materiālu un griešanas metožu izpēte ievērojami uzlabos ražu un kvalitāti.
Efektivitātes uzlabošana:
Jaunās vafeļu griešanas iekārtas būs vērstas uz viedu un automatizētu dizainu. Uzlabotu vadības sistēmu un algoritmu ieviešana ļaus iekārtām automātiski pielāgot griešanas parametrus dažādiem materiāliem un dizaina prasībām, tādējādi ievērojami uzlabojot ražošanas efektivitāti. Izšķiroša loma efektivitātes uzlabošanā būs tādām inovācijām kā vairāku vafeļu griešanas tehnoloģija un ātras asmeņu nomaiņas sistēmas.
Izmaksu samazināšana:
Izmaksu samazināšana ir galvenais virziens vafeļu griešanas tehnoloģijas attīstībā. Attīstoties jauniem materiāliem un griešanas metodēm, paredzams, ka iekārtu izmaksas un uzturēšanas izdevumi tiks efektīvi kontrolēti. Turklāt ražošanas procesu optimizēšana un brāķu samazināšana vēl vairāk samazinās atkritumus ražošanas laikā, tādējādi samazinot kopējās ražošanas izmaksas.
Viedā ražošana un lietu internets (IoT):
Viedās ražošanas un lietu interneta (IoT) tehnoloģiju integrācija ieviesīs revolucionāras pārmaiņas vafeļu griešanas tehnoloģijā. Pateicoties ierīču savstarpējai savienojamībai un datu apmaiņai, katru ražošanas procesa soli var uzraudzīt un optimizēt reāllaikā. Tas ne tikai uzlabo ražošanas efektivitāti un produktu kvalitāti, bet arī sniedz uzņēmumiem precīzāku tirgus prognozēšanu un lēmumu pieņemšanas atbalstu.
Nākotnē vafeļu griešanas tehnoloģija sniegs ievērojamus panākumus precizitātes, efektivitātes un izmaksu ziņā. Šie sasniegumi veicinās pusvadītāju nozares turpmāku attīstību un sniegs cilvēku sabiedrībai vairāk tehnoloģisku inovāciju un ērtību.
Publicēšanas laiks: 2024. gada 19. novembris